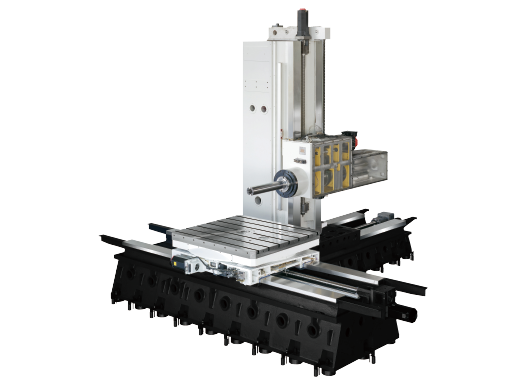
High Rigidity, High Precision
Tough, rugged and durable for PBM series
1. Oversized column design
For greater stability during cutting
Span between box guideways: 780mm
Box guideway thickness: 100mm
Box guideway surface width: 180mm
2. Specially design on front & rear base structure
Widen base design, span between box guideways 1140mm
Box guidway width: 200mm (front base)
Box guidway width: 250mm (rear base)