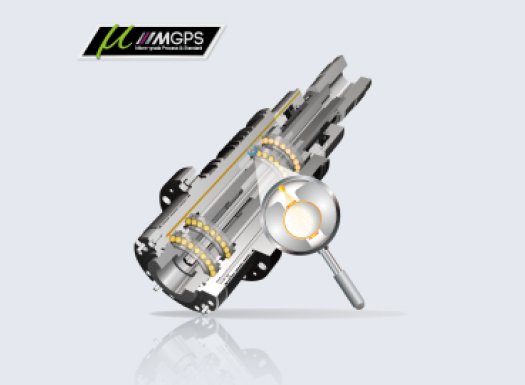
MGPS (Micro-Grade Process and Standard) and High Efficient Spindle
μ-grade accuracy performance, 24hrs spindle operation
1. High quality self-made spindle to ensure spindle run-out within 5μm.
2. Oil-air lubrication spindle:Spindle bearing is lubricated by lubrication oil, spindle is capable of long term running.